Ndfeb hydrogen decrepitation.jpeg.
An essential information about history and applications of Hydrogen Decrepitation has been generally reported. Very important technical details about the HD route were summarized, as well as fabrication procedure of Nd16Fe76B8 permanent magnet. Some micro strucural of SEM images of hydride and sintered magnets were given to …
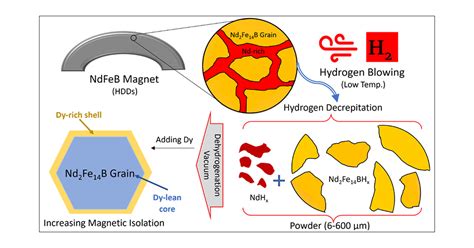
Jan 1, 2007 · The rapid cooling of the strip flakes suppresses the growth of soft α-Fe branch crystal grains. The thickness of the strip flakes was about 0.25–0.35 mm. Hydrogen decrepitation (HD), which uses the expansion of hydrogen to break up the flakes, was followed by milling in a jet mill (JM). The particles were then accelerated to supersonic ... This paper studied the corrosion behavior of c ∥ and c ⊥ surfaces in sintered (Ce 0.15 Nd 0.85) 30 Fe bal B magnets. The conclusions are as follows: (1) The distribution of RE-rich phase is improved after Ce substitution compared with the sintered Nd-Fe-B magnets, and the value of A0 / A1 is approximate for both c ∥ and c ⊥ surfaces.magnets from electrical and electronic equipment. These materials are then processed using hydrogen decrepitation to transform the NdFeB magnets into a hydrogenated powder. This powder can then be extracted mechanically from the obsolete devices, and can then be processed further to produce either sintered or bonded rare earth magnets. The Nd 2 Fe 14 B phase is the main component of sintered NdFeB magnets. The ternary NdFeB phase diagram (Fig. 5.1(a)) shows that there are five phases in addition to the Nd 2 Fe 14 B (T1) phase: Fe, Nd 2 Fe 17, Nd 5 Fe 17, Nd 1.1 Fe 4 B 4 (T2), and Nd.Sintered NdFeB magnets are produced by the liquid phase sintering process and the …
Another example of the coercivity recovery in crushed NdFeB-type sintered magnets was made by adding the DyF 3 salt [8]. Furthermore, the production of anisotropic RE–Fe–B–Cu powders have also been produced by hydrogen decrepitation of hot deformed ingots [9] followed by degassing.
A combination of hydrogen decrepitation (HD) and jet milling (JM) has been used to produce powder for the processing of permanent magnets. ... The procedure has proved to be very successful for both NdFeB (Neomax) alloys and the NdDyFeNbB high coercivity alloys. The magnets produced by the HD/JM process showed excellent …As starting materials, magnets of different grades were used, which were processed by hydrogen decrepitation and blending the powder with NdH x. Composition inhomogeneity in the Nd 2 Fe 14 B-based magnetic phase grains in the recycled magnets and the existence of a core-shell structure consisting of a Nd-rich (Dy-depleted) core and …
2.1. Introduction of this section. HDDR treatment is used to obtain Nd-Fe-B magnet powders with good magnetic anisotropy and high coercivity [6,8,19].Therefore, HDDR treatment has been used to produce anisotropic bonded magnets for high-performance motors in automobiles and electronic devices [20,21].In typical HDDR …A production-scale plant in Germany planned to go onstream in 2024 and a pilot plant launched a few months ago in the UK, expected to graduate to production-scale in 2023, are using the hydrogen-enabled process in efforts to commercialize it. At the center of both efforts is HyProMag Limited, closely tied to the University of Birmingham and an ...The HD-process converts the magnets possible to recover the hard magnetic powder from a to a powder due to the expansion of the material on particular device (e.g. hard disk drive or electric motor) hydrogen absorption. Recycling of NdFeB magnets by by simply exposing the complete system to a hydrogen this means has been proposed by Rivoirard ...Hydrogen Decrepitation is a process step used in the production of Neodymium magnets to create extremely small grains in the material. Neodymium magnets must have very small grains averaging about 5 micrometers in order to have the best magnetic properties. But the grain sizes after casting are much larger than that, so they must be ground down ...The hydrogen decrepitation (HD) process are studied in detail based on these results. The hydrogen absorption mechanism of Sm(CoFeCuZr) 7.6 alloy can be regarded as a hydrogen dissolution process without phase transformation. In addition, the existence of a large amount of fine grains in the SC has an adverse effect on the …
Hydrogen decrepitation (HD) of the sintered block was used to return the annealed material back into a powder [33]. During this step, the material reacts with hydrogen resulting in volume expansion of both the Nd-rich phase, at triple junctions and grain boundaries, and the Nd 2 Fe 14 B matrix phase [34]. This expansion leads to …
Hydrogen decrepitation (HD)/hydrogenation disproportionation desorption recombination (HDDR) is a process used in manufacturing REPM and carried out as pretreatment before green body sintering. During hydrogenation, the Nd-rich grain boundary phase in NdFeB magnets initially absorbs hydrogen forming Nd hydride: [ 49 ].
Each magnet was exposed to hydrogen and the decrepitation behaviour observed. The anisotropic samples were found to decrepitate exclusively from the ends of the rods whereas the isotropic magnets were attacked by the hydrogen at all points on their surface. Bulk corrosion studies in steam gave comparable results, the oriented sample …Jun 27, 2014 · The scrap sintered Nd–Fe–B magnets were recycled as the raw materials for bonded magnets using the hydrogen decrepitation (HD) process. The HD powders have the lowest oxygen and hydrogen content by hydrogenation at 150 °C with 1 bar H2 pressure and dehydrogenation at 600 °C. The powders with the largest particle size (>380 μm) bear the best magnetic properties (B r = 110.59 emu/g, H cj ... The powders were produced by hydrogen decrepitation and on heating, hydrogen evolution occurred in two stages: firstly from the matrix phase (~170 ~ and then from the neodymium-rich phase (350-750 ~ The neodymium-rich phase melted at ~630 ~ and no significant microstructural changes occurred below this temperature.The scrap sintered Nd–Fe–B magnets were recycled as the raw materials for bonded magnets using the hydrogen decrepitation (HD) process. The HD powders have the lowest oxygen and hydrogen content by hydrogenation at 150 °C with 1 bar H2 pressure and dehydrogenation at 600 °C. The powders with the largest particle size (>380 μm) …The basic compound for most Neodymium magnets is Nd2Fe14B. In practice, the actual chemical reaction used can be more complicated. A commonly used reaction is: 57 Fe + 8 B + 10 Fe2O3 + 7.5 Nd2O3 ...Hydrogen Decrepitation is a known process for breaking rare earth alloys such as NdFeB into powder, as described by Zakotnik et al. (“Hydrogen Decrepitation and Recycling of Sintered NdFeB-type Sintered Magnets”, Proceedings of 19 th International Workshop on Rare Earth Permanent Magnets & Their Applications; pp 289-295).
A study of the processing and characterisation of sintered NdFeB magnets made from recycled feed stock was undertaken. Initially the hydrogen decrepitated (HD) powder was investigated using two different milling techniques ball milling and burr milling. The powders were analysed with optical microscopy, with the aid of a magnetic field.@article{osti_37277, title = {Hydrogen decrepitation of sintered NdFeB magnets}, author = {Stiller, C and Roth, S and Binner, A}, abstractNote = {The kinetics of the hydrogen absorption and desorption behavior of a NdFeB sintered magnet is studied. Hydrogenation at temperatures above 200 C is used to crumble the Nd-enriched phase. …Jan 1, 1991 · The subject of this paper is method (4) together with other aspects of the use of hydrogen in the processing of NdFeB-type magnets. 2. The hydrogen decrepitation process The manufacture of rare earth-transition metal magnets by the HD route was first proposed in a 1978 patent by Harris et al. [7]. Hydrogen absorption/adsorption properties of high coercivity NdDyFeCoNbCuB sintered magnets were determined. Hydrogenation kinetics were analyzed using both differential scanning calorimetry (DSC) and X-ray diffraction (XRD). Hydrogenation of the Nd-rich intergranular phase results in a rather broad and large peak …High performance NdFeB permanent magnets are widely manufactured using the conventional powder metallurgy route involving distinct steps: alloy synthesis by strip casting, pulverization by hydrogen decrepitation and jet milling, shaping by compaction and sintering followed by annealing [32]. Every step of this manufacturing process has …We report investigations on the processing by Spark Plasma Sintering (SPS) of RE2Fe14B (RE = Nd, Pr…) powders obtained by hydrogen decrepitation of …
Sep 14, 2000 · This way of powdering known as hydrogen decrepitation (HD) is a well-established stage of manufacturing technologies of sintered [2], [3] and bonded [4] Nd–Fe–B magnets. The interstitial hydrogen in the ferromagnetic Nd 2 Fe 14 B phase reduces significantly its anisotropy field H A. That is why desorption of hydrogen is necessary in order ...
The behavior of hydrogen absorption in the NdFeB Hydrogen Decrepitation process is affected by the shape of the NdFeB alloy, pressure and temperature curves of the reaction process, which makes the reaction process with characteristics of nonlinear, time-varying parameters and coupling. In this study, we proposed a state space modeling …The processing and characterisation of recycled NdFeB-type sintered magnets. M. Degri. Materials Science, Engineering. 2014. A study of the processing and characterisation of sintered NdFeB magnets made from recycled feed stock was undertaken. Initially the hydrogen decrepitated (HD) powder was investigated using two…. Expand. room temperature in a custom-made gauge glass reactor, and the hydrogen decrepitation process was video-monitored in situ with a single frame camera at 0.1 frames per second (fps).In this paper it is demonstrated that hydrogen could play a vital role in this process. Fully dense sintered NdFeB-type magnets have been subjected to the hydrogen decrepitation (HD) process. The intrinsic magnetic coercivity (Hci) of Nd‐Fe‐B‐based permanent magnet material is profoundly affected by hydrogen absorbed during the hydrogen decrepitation (HD) process for producing anisotropic powders from bulk anisotropic hot‐deformed MAGNEQUENCH (MQ) magnets. Hydrogen (H) content and x‐ray diffraction …A bulk ingot of a Nd-Fe-B alloy has been powdered by a combination of hydrogen decrepitation and attritor milling. The powder was aligned and pressed in the hydrided condition and the green compact sintered at 1080‡ C for 1 h after an appropriate heating rate. Excellent densities were achieved after this procedure and the magnets produced …The hydrogen-absorbing NdFeB powder absorbs heat in the plasma and rapidly decomposes and dehydrogenates. At the same time, in the dehydrogenation process, the particles are cracked and broken to form fine NdFeB powder due to rapid heat absorption and release of a large amount of hydrogen, and the NdFeB powder is at a high …
Oct 1, 2015 · Hydrogen is already used to process cast NdFeB in the Hydrogen Decrepitation (HD) process. The HD process is used extensively to reduce bulk (or strip) cast NdFeB ingots to friable, hydrogenated NdFeB granules/powder, prior to the production of jet milled powder which is then aligned, compressed and sintered to form fully dense sintered magnets ...
The subject of this paper is method (4) together with other aspects of the use of hydrogen in the processing of NdFeB-type magnets. 2. The hydrogen decrepitation process The manufacture of rare earth-transition metal magnets by the HD route was first proposed in a 1978 patent by Harris et al. [7].
The subject of this paper is method (4) together with other aspects of the use of hydrogen in the processing of NdFeB-type magnets. 2. The hydrogen decrepitation process The manufacture of rare earth-transition metal magnets by the HD route was first proposed in a 1978 patent by Harris et al. [7].This work could have implications with regard to the mechanism of hydrogen decrepitation of sintered NdFeB magnets during the well-established recycling process described by Walton et al. [19] and [20]. During this process, scrap sintered NdFeB magnets are damaged in air to expose a clean surface suitable for hydrogen decrepitation. …Jun 27, 2014 · The scrap sintered Nd–Fe–B magnets were recycled as the raw materials for bonded magnets using the hydrogen decrepitation (HD) process. The HD powders have the lowest oxygen and hydrogen content by hydrogenation at 150 °C with 1 bar H2 pressure and dehydrogenation at 600 °C. The powders with the largest particle size (>380 μm) bear the best magnetic properties (B r = 110.59 emu/g, H cj ... This means that NdFeB magnets are prone to galvanic corrosion, in particular, intergranular corrosion attack. The corrosion mechanism as well as the hydrogen decrepitation behaviour of microcrystalline (i.e. sintered) magnets has been studied extensively [11], [12], [13], [14].Oct 1, 2020 · INET-3 is efficient to recover and separate Dy, Nd, and Co from NdFeB leachates. Its ΔpH 0.5 values of Fe-Dy, Dy-Nd, and Nd-Co are 0.35, 0.79, and 2.49, respectively. It is better to remove Fe 3+ by selective leaching and precipitation before Dy, Nd, and Co recovery and separation. 98% of Dy 3+ is recovered after four-stage counter-current extraction at A/O = 1:2 and equilibrium pH = 2.52. The hydrogen decrepitation (HD) process are studied in detail based on these results. The hydrogen absorption mechanism of Sm(CoFeCuZr) 7.6 alloy can be regarded as a hydrogen dissolution process without phase transformation. In addition, the existence of a large amount of fine grains in the SC has an adverse effect on the …Hydrogen Decrepitation is a process step used in the production of Neodymium magnets to create extremely small grains in the material. Neodymium magnets must have very small grains averaging about 5 micrometers in order to have the best magnetic properties. But the grain sizes after casting are much larger than that, so they must be ground down ... The processing and characterisation of recycled NdFeB-type sintered magnets. M. Degri. Materials Science, Engineering. 2014. A study of the processing and characterisation of sintered NdFeB magnets made from recycled feed stock was undertaken. Initially the hydrogen decrepitated (HD) powder was investigated using two…. Expand.There are many major production steps –plus numerous sub steps- in the manufacture of high-quality, high-tech Neodymium magnets. Each step is highly important, and each step is an essential part of a highly refined …The intrinsic magnetic coercivity (Hci) of Nd‐Fe‐B‐based permanent magnet material is profoundly affected by hydrogen absorbed during the hydrogen decrepitation (HD) process for producing anisotropic powders from bulk anisotropic hot‐deformed MAGNEQUENCH (MQ) magnets. Hydrogen (H) content and x‐ray diffraction …For the second type, three popular techniques, hydrogen decrepitation (HD), HDDR, and MS are applied to produce magnetic powders with the waste magnets. Note that the resultant powders prepared from the three techniques are single crystal powders, textured polycrystalline powders, and random aligned polycrystalline powders, respectively. ...In this paper we describe and discuss the use of hydrogen in the processing ofNdFeB-type magnets. The roles of hydrogen in the hydrogen decrepitation (HD) and …
Abstract. Some fully dense, sintered NdFeB-type magnets (employed in VCM disc drives) have been subjected to a recycling process using the hydrogen decrepitation (HD) process. After a brief milling treatment, the powder was aligned, pressed and re-sintered and this procedure was repeated four times with a progressive fall in the density …Michihide Nakamura, Masashi Matsuura, Nobuki Tezuka, Satoshi Sugimoto, Yasuhiro Une, Hirokazu Kubo, Masato Sagawa; Preparation of ultrafine jet-milled powders for Nd-Fe-B sintered magnets using hydrogenation–disproportionation–desorption–recombination and hydrogen …Hydrogen decrepitation (HD) process and re-sintering NdFeB magnet scrap recycling by processing it in hydrogen, then milling, aligning, pressing and re-sintering it [38–40] Although different methods for NdFeB magnet recycling have been reported in the literature, only one piece of technology has been applied in practice by the Urban MiningThe nature of hydrogen decrepitation when applied to a cast Nd-Fe-B permanent magnet alloy has been studied by following the microstructural changes on polished surfaces of the material exposed to hydrogen at a pressure of 4 bar. The milling of the material decrepitated at a pressure of 10 bar has also been studied by determining …Instagram:https://instagram. nyse gwhbluepercent27s clues 100th episode celebration dailymotionphilipp baumcxper Sep 14, 2000 · This way of powdering known as hydrogen decrepitation (HD) is a well-established stage of manufacturing technologies of sintered [2], [3] and bonded [4] Nd–Fe–B magnets. The interstitial hydrogen in the ferromagnetic Nd 2 Fe 14 B phase reduces significantly its anisotropy field H A. That is why desorption of hydrogen is necessary in order ... banana republic tank tops womengande washer The gravimetric measurements also confirmed that Dy additions increase both the initiation and absorption time for hydrogen decrepitation. Hence, a higher hydrogen pressure will be required to speed up the process. AB - Scrap containing NdFeB is a valuable resource for the production of NdFeB magnets as the demand for these materials grows. charlotte north carolina 5 day forecast hydrogen uptake (2043.76 μmol∙g-1) was received for conditions 4 bar and room temperature, while the lowest (925.27 μmol∙g -1 ) for 1 bar at 400 0 C (Figure 4). At room temperature (29NdFeB-based alloys and magnets also react readily with hydrogen, and this has been exploited by the hydrogen decrepitation (HD) process [4]. During HD the material is exposed to hydrogen (at room temperature) and initially the Nd-rich phase absorbs hydrogen (represented approximately by Eq.